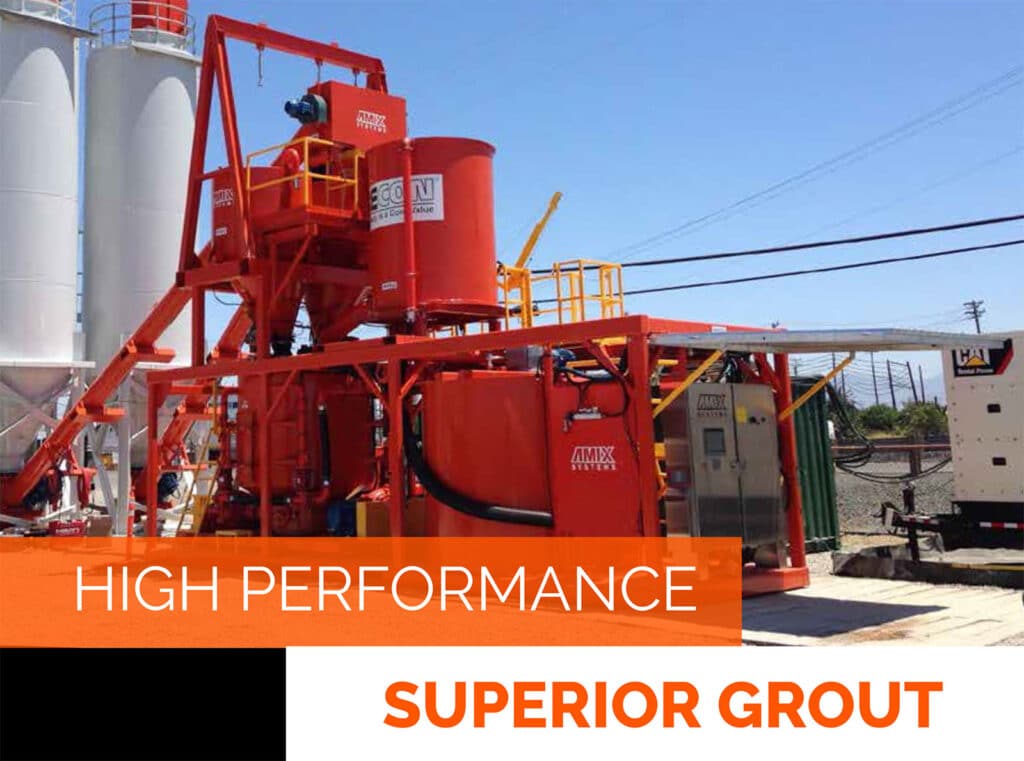
Book a discovery call with Ben MacDonald to learn how Amix Systems can transform your next project.
Grout mixing plants play a crucial role in the mining and construction industry. If you want to ensure that your grouting applications run efficiently and effectively, understanding the design aspects of these plants is essential. An important component of this is the cement mixer design. The right design can lead to better mixing efficiencies, improved durability, and enhanced operational effectiveness.
The term cement mixer design encompasses various engineering elements needed to create equipment that meets the demands of today’s construction environments. Key considerations in cement mixer design include the size and shape of the mixer drum, the type of mixing blades used, and the overall configuration of the components. Each of these factors can significantly impact the mixing capabilities and efficiency of the equipment.
Innovative Engineering Solutions
When it comes to designing grout mixing plants, innovative engineering solutions are key. Companies like AMIX Systems specialize in creating high-performance grout mixing plants and batch systems using advanced engineering software and fabrication tools. This approach ensures that you receive reliable and efficient equipment tailored to your specific needs.
One vital feature of an effective grout mixing plant is the ability to streamline processes and improve workflow. The design should incorporate aspects such as:
Feature | Description |
---|---|
Modular Design | Allows for easy expansion or modification of the plant |
Efficient Layout | Streamlines operations and minimizes material handling |
High-Performance Components | Ensures longevity and reliability of the equipment |
By focusing on these design principles, you can enhance your grout mixing efficiency and maintain the quality of your mixtures.
Automation Expertise
Automation is another essential factor when designing grout mixing plants. You can benefit significantly from systems equipped with advanced automation features that enhance control and precision throughout the mixing process. The team at AMIX Systems boasts over 20 years of experience in PLC programming and motor control assembly, making them experts in integrating automation into grout mixing control systems.
Key benefits of implementing automation in your grout mixing plants include:
Benefit | Description |
---|---|
Real-Time Monitoring | Allows for immediate adjustments and quality control |
Reduced Labor Costs | Minimizes the need for manual oversight |
Enhanced Process Consistency | Provides uniform mixing results, ensuring quality |
By integrating automation into your grout mixing plant, you can improve both the efficiency and accuracy of your grouting applications, ultimately leading to better project outcomes.
For more about specific cement mixer designs and equipment, explore our sections on various types of grout pump mixer, concrete mixing equipment, and cement grout injection.
Retrofitting Services Offered
As a geotechnical engineer or construction supervisor, you may be aware that enhancing your existing systems can lead to significant improvements in efficiency and performance. Retrofitting services can optimize your grout mixing plants and batch systems, ensuring that they meet your growing operational needs.
Enhancing Batch Systems
Upgrading your batch systems is a crucial step in boosting productivity. Companies like AMIX Systems specialize in designing and fabricating high-performance workspace solutions. They use cutting-edge engineering software and fabrication tools to tailor systems specifically to your requirements.
The benefits of enhancing your batch systems include:
Improvement Area | Potential Benefits |
---|---|
Efficiency | Improved throughput and reduced operational delays |
Reliability | Enhanced durability and decreased downtime for repairs |
Adaptability | Systems can be customized to accommodate various grout types |
With these enhancements, your grout mixing capabilities will become more responsive, allowing you to tackle diverse projects with greater ease.
Improving Productivity
Once your batch systems are optimized, focusing on productivity enhancements will refine your operational effectiveness further. Retrofitting existing grout mixing plants enables you to leverage the knowledge of current systems to identify and implement upgrades that maximize performance.
Here are some of the ways retrofitting can improve productivity:
Strategy | Expected Outcome |
---|---|
Updating Equipment | Improved mixing consistency leads to higher quality grout |
Implementing Automation | Reduced manual labor, lower error rates, and faster production times |
Enhancing Communication Tools | Better coordination among teams, leading to smoother workflows |
By investing in retrofitting services, you can ensure that your operations run smoothly, delivering high-quality results while meeting demanding project timelines.
For more information on grout mixing solutions, consider exploring various options like grout mixer pumps or high pressure cement grouting pumps. Prioritizing upgrades in your equipment will lead to long-term benefits for your projects and the overall efficiency of your operations.
Emphasizing Performance and Reliability
In the grouting industry, it’s essential to have reliable products that meet your specific needs. The design and function of your cement mixers can significantly impact your project’s success. Let’s explore some of the key aspects of reliable products for grout mixing and discuss how you can ensure cost-effective operations.
Reliable Products for Grout Mixing
When choosing equipment for grout mixing, reliability is paramount. AMIX Systems specializes in designing and fabricating high-performance grout mixing plants that are built to last. Their expertise in using cutting-edge engineering software ensures that you receive a product that meets the highest standards of durability and efficiency.
Product Type | Features | Benefits |
---|---|---|
Grout Mixer Pump | High performance, custom design | Reliable mixing and pumping efficiency |
Continuous Cement Mixer | Consistent mix quality | Ideal for large projects with high-volume requirements |
High Pressure Cement Grouting Pump | Efficient pressure control | Enhances workability and placement |
With AMIX Systems’ products, you can feel confident that your grout mixing operations will run smoothly. Their team has over 20 years of experience in PLC programming and motor control assembly, providing you with industry knowledge that translates into superior products.
Cost-Effective Operations
Running a cost-effective operation involves more than just investing in quality equipment. It’s about maximizing efficiency and minimizing waste. AMIX Systems offers plant retrofitting services tailored to enhance the productivity and reliability of your grout plants. By leveraging existing batch systems, you can achieve greater results without the need for a complete system overhaul.
Some of the cost-saving measures you can implement include:
- Optimize Batch Systems: Focusing on efficient batch management can significantly reduce material waste.
- Regular Maintenance: Keeping your equipment in top condition extends its lifespan and performance.
- Investing in Automation: Automating processes can help reduce labor costs and enhance precision.
For those seeking to understand specific needs related to grouting, consider exploring products like the grout injection pump and grout mixer pump, which provide exceptional performance and reliability.
In conclusion, a well-thought-out cement mixer design is central to the success of any grout mixing operation. By emphasizing the importance of a robust design, investing in reliable equipment, and leveraging automation, companies can achieve significant enhancements in their grouting processes. The ideal cement mixer design not only ensures high-quality mixtures but also translates into improved project outcomes and operational efficiencies. Therefore, understanding and implementing the right cement mixer design strategies can greatly enhance your competitive position in the mining and construction sectors.
Book A Discovery Call
Empower your projects with efficient mixing solutions that enable scalable and consistent results for even the largest tasks. Book a discovery call with Ben MacDonald to discuss how we can add value to your project:
Email: info@amixsystems.com – Phone: 1-604-746-0555
Postal Address: Suite 460 – 688 West Hastings St, Vancvouver, BC. V6B 1P1