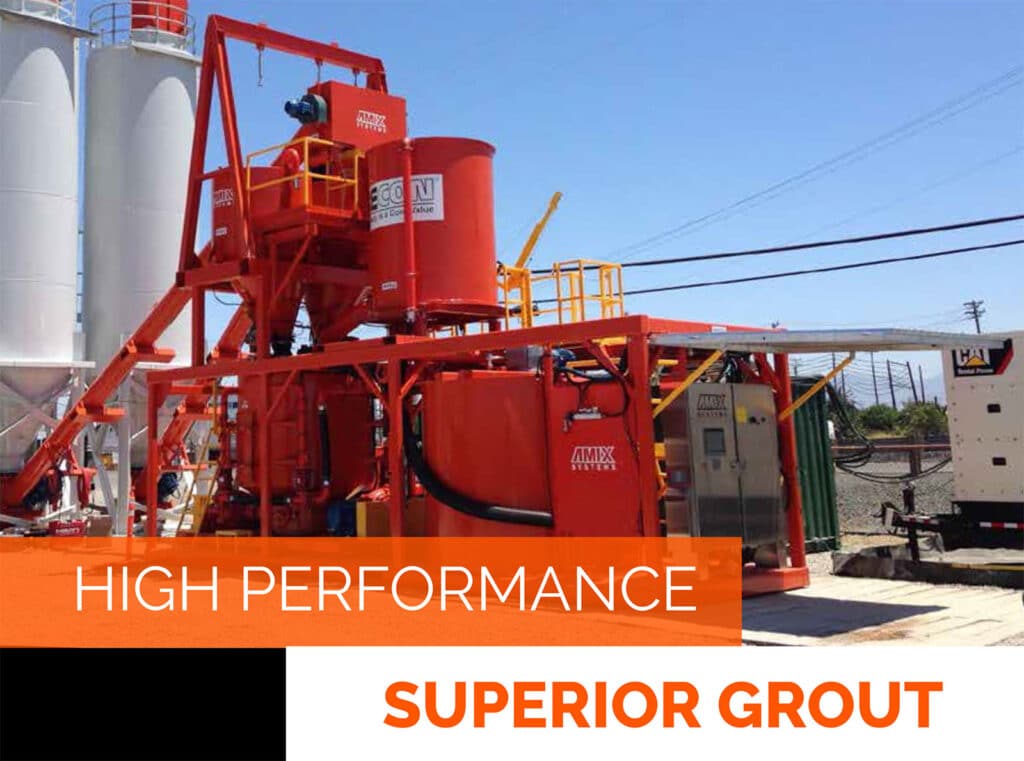
Book a discovery call with Ben MacDonald to learn how Amix Systems can transform your next project.
An overview of grout plants
Grouting plant equipment plays a crucial role in the construction, mining, and civil engineering industries. These specialized machines are designed to mix and pump grout, a fluid material used to fill gaps, strengthen structures, and stabilize soil. The proper selection and use of grouting plant equipment can significantly impact the success of a project, improving efficiency, cost-effectiveness, and overall results.
The Importance of Grouting Plant Equipment
Grouting plant equipment is essential for various applications, including:
- Reinforcing structures: Grout is used to fill cracks and voids in bridges, buildings, and other structures, enhancing their strength and durability.
- Stabilizing ground: Grouting helps to stabilize soil and rock, preventing landslides, sinkholes, and other geotechnical issues.
- Waterproofing: Grout is used to seal joints and cracks in tunnels, dams, and reservoirs, preventing water leakage and erosion.
- Improving foundations: Grouting can increase the bearing capacity of building foundations, allowing them to support heavier loads.
- Filling voids: Grout is used to fill empty spaces in construction projects, ensuring stability and preventing settling.
Investing in high-quality grouting plant equipment is essential for achieving optimal results in these applications. The right equipment can improve accuracy, speed, flexibility, durability, and cost-effectiveness, ultimately contributing to the success of a project.
Key Features of Grouting Plant Equipment
When selecting grouting plant equipment, it is important to consider the following key features:
Efficiency and Productivity
High-performance grouting plant equipment is designed to maximize efficiency and productivity on the job site. Advanced automation features allow for precise control and monitoring of the grout mixing process, minimizing downtime and ensuring consistent grout quality. High-shear mixing technology can significantly reduce mixing time while maintaining a uniform grout mixture. Continuous operation capabilities enable uninterrupted grouting, further enhancing productivity.
Customization Options
Grouting plant equipment should be customizable to meet the specific requirements of each project. Adjustable mixing speeds allow for fine-tuning grout consistency, while variable tank sizes accommodate projects of different scales. Specialized pumping systems can be tailored to handle unique project demands, such as high-pressure or long-distance grouting.
Durability and Reliability
Grouting plant equipment must be built to withstand the harsh conditions of construction, mining, and civil engineering projects. High-quality materials and robust construction ensure long-lasting performance and minimal downtime. Smart design features, such as replaceable wear parts and easy-access maintenance points, can further extend the lifespan of the equipment.
Cost-Effectiveness
While high-performance grouting plant equipment may require a higher initial investment, it can provide significant long-term cost savings. Durable, reliable equipment requires less maintenance and fewer repairs, reducing overall operating costs. The increased efficiency and productivity of high-performance equipment can also lead to faster project completion times, resulting in additional cost savings.
Backfill Systems and Environmental Considerations
Backfill systems are an essential component of many construction, mining, and civil engineering projects. These systems are used to refill excavated areas around foundations, utilities, and other structures, providing stability and support. When selecting and using backfill systems, it is important to consider both the effectiveness of the backfilling technique and its environmental impact.
Backfilling Techniques
There are several common backfilling techniques, each with its own advantages and use cases:
- Compacted fill: This method involves placing fill material in layers and compacting each layer to eliminate air pockets and ensure maximum stability. Compacted fill is often used for foundations and road bases.
- Slurry backfill: This technique uses a mixture of water and particulate material to create a slurry that fills all voids and hardens over time. Slurry backfill is commonly used for underground structures and trenches.
- Flowable fill: Also known as controlled low-strength material (CLSM), flowable fill is a self-compacting, low-strength material that is easy to place and requires minimal labor. It is often used in utility trenches and areas with difficult access.
Environmental Impact
As environmental sustainability becomes increasingly important in the construction and mining industries, it is crucial to consider the ecological footprint of backfilling operations. Some strategies for reducing environmental impact include:
- Material selection: Using recycled materials, such as crushed concrete or industrial by-products, can reduce waste and minimize the need for virgin materials.
- Water management: Proper management of water used in slurry or flowable fill methods can prevent contamination of local water sources. Filtration systems can help to remove contaminants before the water is released back into the environment.
- Energy efficiency: Modern backfilling equipment is designed to be energy-efficient, reducing fuel consumption and emissions. Choosing equipment with a low environmental impact can contribute to the overall sustainability of a project.
By carefully considering backfilling techniques and their environmental impacts, project managers can ensure that their backfilling operations are both effective and sustainable.
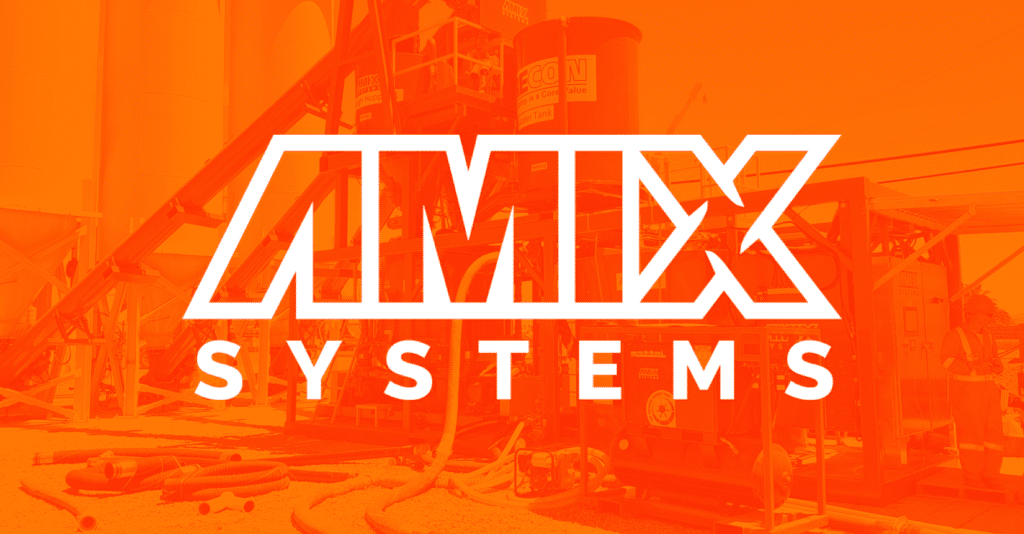
Maintaining Grouting Plant Equipment
Regular maintenance is essential for ensuring the longevity and optimal performance of grouting plant equipment. A well-maintained machine will operate more efficiently, require fewer repairs, and provide more consistent results.
Regular Inspections
Scheduled inspections can help to identify potential issues before they lead to costly breakdowns. Key components to inspect include:
- Hydraulic systems: Check for leaks and ensure that fluid levels are within the recommended range.
- Electrical components: Inspect wires and connections for signs of wear or damage.
- Mechanical parts: Pay close attention to moving parts, particularly those exposed to abrasive materials.
- Safety features: Ensure that all safety devices and emergency stop mechanisms are functioning properly.
Cleaning and Lubrication
Regular cleaning and lubrication can prevent the buildup of debris and reduce wear on critical components. Some best practices include:
- Daily rinsing: Rinse mixing tanks and hoppers after each use to prevent material buildup.
- Weekly deep cleaning: Use a pressure washer to remove stubborn debris from hard-to-reach areas.
- Periodic disassembly: Occasionally disassemble key components for thorough cleaning and inspection.
- Lubrication: Follow the manufacturer’s recommendations for lubricating moving parts to minimize friction and wear.
Spare Parts and Upgrades
Keeping a stock of critical spare parts on hand can minimize downtime in the event of a breakdown. Additionally, consider upgrading components as newer, more efficient options become available. This can help to improve the performance and longevity of the equipment.
Selecting the Right Grouting Plant Equipment
Choosing the right grouting plant equipment is crucial for the success of a project. Some key factors to consider include:
Performance and Consistency
Equipment should be capable of mixing and pumping grout at high speeds while maintaining a consistent mix quality. High-performance colloidal grout mixers are particularly well-suited for this purpose.
Durability and Reliability
Equipment should be constructed from high-quality materials that can withstand the rigors of the job site. Look for machines with a proven track record of reliable performance.
Customization Options
The ability to customize equipment to meet the specific needs of a project can greatly enhance its effectiveness. Look for machines with adjustable settings and interchangeable components.
Cost-Effectiveness
While initial cost is important, it is also essential to consider the long-term cost of ownership. High-quality equipment may have a higher upfront cost but can provide significant savings in terms of reduced maintenance and repair costs over its lifespan.
Environmental Impact
Whenever possible, choose equipment that minimizes environmental impact, such as machines with efficient backfilling systems and low emissions.
Final Thoughts on Grouting Plant Equipment
Investing in the right grouting plant equipment is essential for the success of any construction, mining, or civil engineering project. By prioritizing key features such as efficiency, customization options, and durability, project managers can ensure that their equipment provides optimal performance and cost-effectiveness.
Additionally, considering the environmental impact of backfill systems and implementing sustainable practices can help to minimize the ecological footprint of a project.
Regular maintenance, including inspections, cleaning, and lubrication, is crucial for ensuring the longevity and reliability of grouting plant equipment.
When selecting equipment, it is important to consider factors such as performance, consistency, durability, customization options, and cost-effectiveness. By carefully evaluating these factors and choosing equipment that meets the specific needs of a project, managers can maximize the success of their grouting operations.
Contact Amix Systems for Your Grouting Plant Equipment Needs
At Amix Systems, we understand the importance of high-quality grouting plant equipment for the success of your projects. With over 25 years of experience in designing and manufacturing automated grout mixing plants, batch systems, and related equipment, we are dedicated to providing innovative, high-performance, and cost-effective solutions for various ground improvement techniques and grouting applications.
Our range of products, including the Amix Colloidal Mixer (ACM), Typhoon Series, Cyclone Series, and Hurricane Series, are designed to meet the unique needs of your projects while delivering exceptional efficiency, reliability, and consistency. We also offer a wide range of accessories, such as grout pumps, agitated tanks, silos and hoppers, feed systems, and more, to provide complete solutions for your grouting operations.
If you have any questions about our grouting plant equipment or would like to discuss your specific project requirements, please don’t hesitate to contact our knowledgeable team. We look forward to helping you find the perfect grouting plant equipment solution for your construction, mining, or civil engineering project.
Book A Discovery Call
Empower your projects with efficient mixing solutions that enable scalable and consistent results for even the largest tasks. Book a discovery call with Ben MacDonald to discuss how we can add value to your project:
Email: info@amixsystems.com – Phone: 1-604-746-0555
Postal Address: Suite 460 – 688 West Hastings St, Vancvouver, BC. V6B 1P1