Projects
Deep soil Mixing Colloidal Grout Plant
AMIX Grout Plant (AGP) was used to eliminate multiple mixing systems, providing high outputs while maintaining a low carbon footprint.
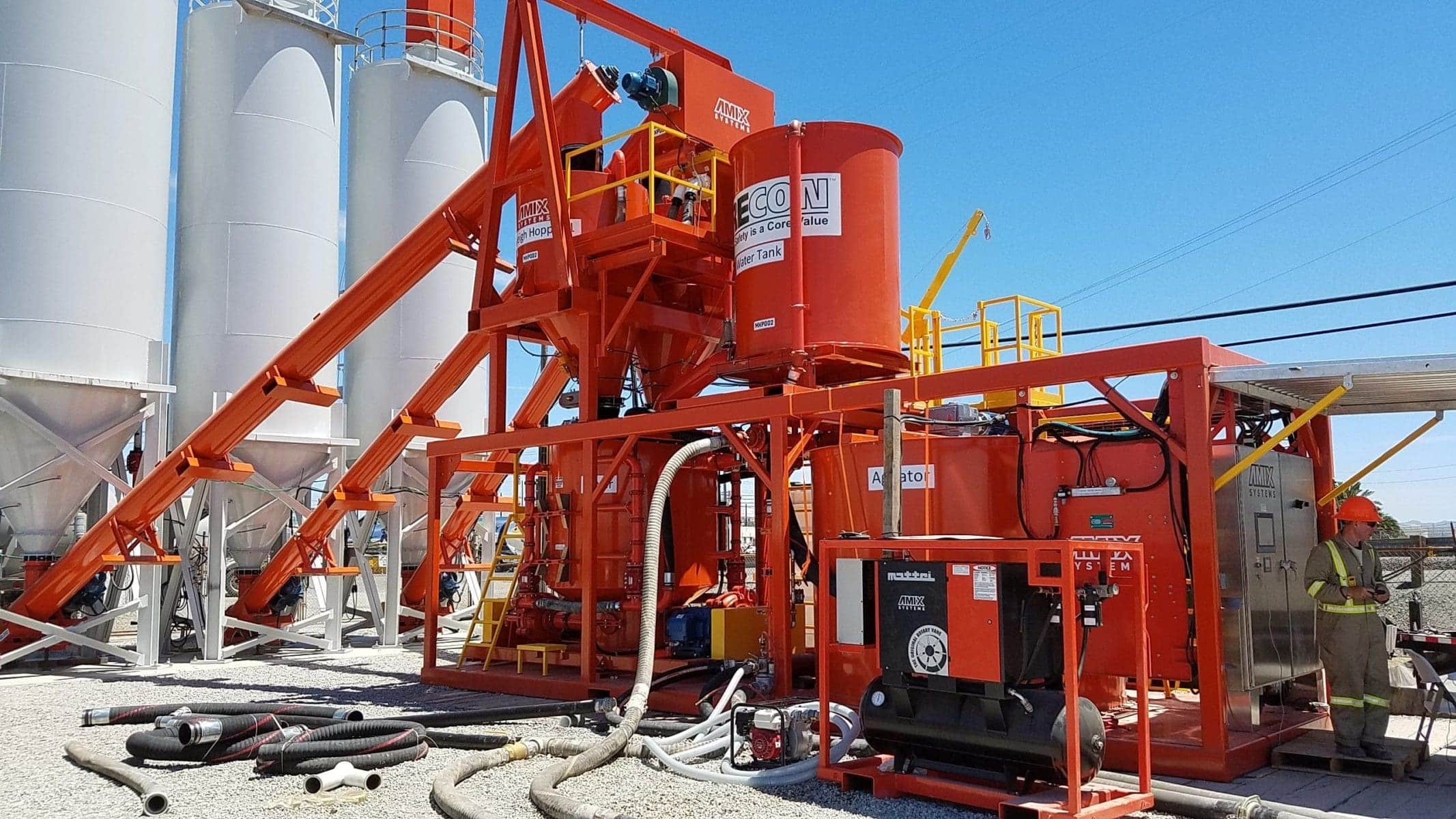
Location
Houston, TX
Products
AGP-Hurricane
Services
Design, Engineering and Fabrication
Completion Date
March 2017
Remedial Construction Services – Tesoro Refinery Martinez, California, U.S.A
Project Description:
RECON Services was tasked with providing a design solution that would enable the site to be ready for development, thus ensuring the potential migration of contaminants from the site was halted. A deep soil mixing method for in-situ remediation and encapsulation of contaminated soils was needed to render the polluted site suitable for the natural environments future use.
Project Scope:
To remediate a plume of underground contaminants inside of an active oil refinery, AMIX Systems was contracted to manufacture a high-shear colloidal grout mixing system that will feed grout for deep soil mixing. The project required a high-efficiency, high-output system while producing superior quality uniform mixes on a short time-line.
The Need:
The job had a fast mobilization date and required a high capacity slurry plant capable of accurately mixing three separate dry bulk components. AMIX Systems designed, manufactured and supplied the AGP Grout Plant within 4 months from start to completion.
AMIX AGP 100 Colloidal Grout System:
- High efficiency
- Fully automated
- Easy to maintain
- High quality control
- Easy to operate
- Self-cleaning
- Modular design
- Low carbon footprint
The Solution
AMIX Systems was an outstanding partner in helping design and build a slurry plant that exceeded RECON’s service needs. The AGP-Colloidal Grout Mixer increased production with mixer capacity of 6 m3 (1,585 gallons) powered by two 8”X4” Colloidal Mill 112 kw (200hp) motors. The AGP gave RECON Services the ability to produce outputs ranging from 100 – 150 m3/hr (139 yd3 /hr).
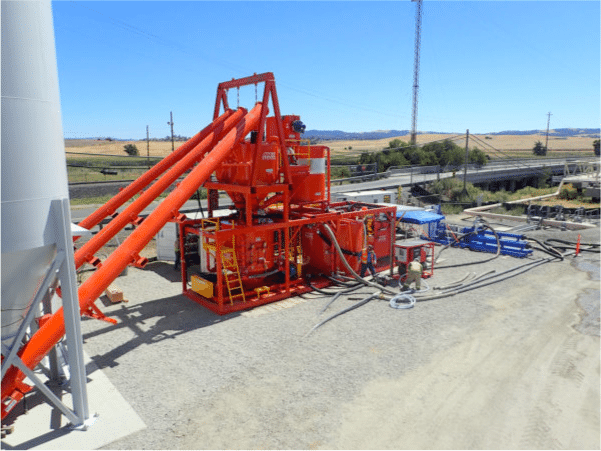
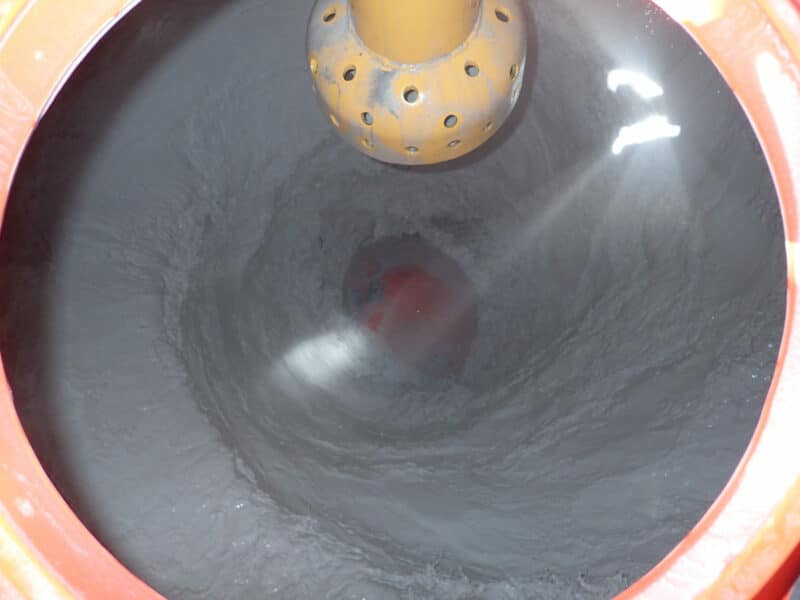
More Accessible
AMIX Grout Plant (AGP) was simple to operate, low maintenance, compact having a low carbon footprint and easily accessible for site set up and mobility.
More Reliable
The AMIX Grout Plant (AGP) allowed RECON to quickly mobilize and maintain a high capacity slurry plant capable of accurately mixing three separate dry bulk components for an aggressive construction schedule.
More Efficient
AMIX Grout Plant (AGP) required little or no operator intervention, minimal clean up, no waste while producing high quality grout mixes within customer specifications.
“There is no better affirmation of satisfaction with a product than by a recommendation to others”. – Jeff Lewman
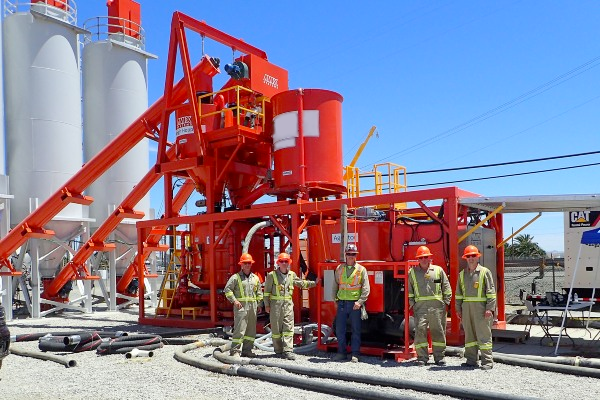
Services and Equipment Provided:
- Conceptual & detailed design, engineering & fabrication of a high sheer colloidal mixing system
- Worked with client to narrow down scope of equipment
- Equipment set up
- Commissioning and personnel training
- Supply of equipment:
– AGP-Colloidal Grout Plant
– AAT Agitation tank
– PLC control system w/ remote access
– Motor control center with NEMA 4X rate enclosure & VFD motor drives
– Pneumatic control system
– Feed System
– Binder weigh hoppers
– Water surge tank
– (3) 150 tonne silos
– Dust collection system
– 50’x75’ equipment skid
The plant has now been in constant use for seven months, operating 10 hours per day, six days per week. RECON has found the plant to be reliable, easy to operate, and easy to keep clean. The plant’s reliability can be proven by a track record of over 150 days of operation, once commissioning was complete, with only 3 down days for maintenance and repair. Its ease of operation has been a positive attribute; new plant operators are trained in as little as a few shifts
Jeff Lewman
Construction Manager , Remedial Construction Services, LP.
Get a quote
If you would like to learn more about this product and receive a quote simple fill out our quote request form.
Email: sales@amixsystems.com – Phone: 1-604-746-0555
Postal Address: Suite 460 – 688 West Hastings St Vancvouver, BC V6B 1P1